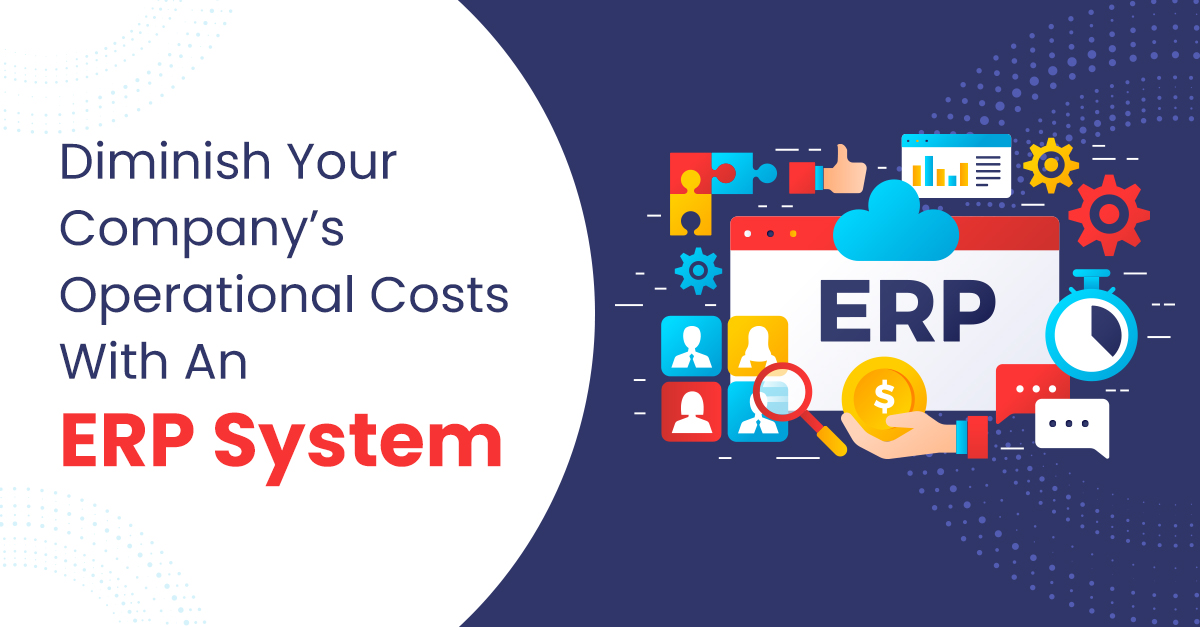
Table of Contents
Reduce operational costs without sacrificing performance…
What Is An ERP System?
Enterprise resource planning (ERP) dictates the core processes and software that a business needs to function appropriately. It encompasses all other facets of the company, combining them into a single centralized system and database. It’s an efficient way to diminish operational costs and boost profit margins within a business.
Despite the fact, that ERP is referred to as a single software, there are varying different shades of ERP systems. Different modules and features are a value-added bonus that is removable concerning ERP software to cater to the unique demands of a business.
The Importance of ERP Systems in Reducing Operational Costs
When custom manufacturing is taken into consideration, the manufacturers are seeking ways to enhance operational efficiencies and eliminate costs while at the same time striving to meet customer needs and business objectives. An ERP system is the core element for custom manufacturers, as an ERP not only helps streamline operations but also reduces costs significantly.
Being a complex process, custom manufacturing involves a series of operations, right from procurement and inventory management to production planning and delivery. An ERP is a requisite as it combines all essential business processes and data into a single platform and delivers a unified operational view. The platform further enables custom manufacturers to manage everything starting from production planning and inventory management to custom relationships and financial management within a single system.
This level of oversight not only helps streamline your production processes but also has an impact on your costs. ERP systems offer accurate, real-time information following daily operations to aid manufacturing companies decline operational costs by nearly 23% and administration costs by about 22%. (Source: Genius ERP)
Innovative Ways ERP System Can Lower Operational Costs
1. Optimized Production Planning
ERP system leverages a centralized platform for custom manufacturers to manage and plan production processes. This, in turn, helps you streamline production schedules. Assign resources more efficiently, and diminish production lead times. A better understanding of the production processes can help you identify occasions for cost savings like lessening material waste and enhancing quality control.
The real-time data following aspects like machine performance, inventory levels, and production schedules, ERP software can help your production manager in driving informed choices that are single-handedly aligned with your company’s goals and objectives- resulting in enhanced effectiveness and lower costs.
2. Streamlined Inventory Management
ERP systems track inventory levels in real-time, which can help you identify inventory shortages and minimize the risk of overstocking- causing minimal wastage and lower storage costs.
ERP real-time insights can help reduce your inventory levels, emancipating capital and lowering the possibility that parts and elements are damageable while lying around the shop corners or a few items will turn obsolete or lie on shelves unused. Advanced ERPs precisely designed for custom manufacturing can forecast inventory needs- as initially as the estimation stage. Accurate forecasting allows you to understand the parts and raw materials you require, delivering you more time to procure items to keep the outlet running effectively and enabling you to buy only and store the products you need.
ERPs help you automate time-consuming processes following inventory like physical inventory counts. The lack of a real-time inventory system might force you to shut down operations to manually count your inventory.
3. Improved Financial Management with ERP System
ERP systems offer custom manufacturers real-time financial data, encompassing cash flow, revenue, and expenses. This will eventually help you spot overspending areas and drive informed choices and decisions to reduce costs. Formulating the right decisions based on precise data will help you sail your company in the right direction, emphasizing profitable jobs and curtailing financially senseless projects.
Accurate financial data can help enhance budgeting and forecasting processes, eliminate the risk of errors, and optimize cash flow management.
It will also help your accounting department to save money using ERP software to automate financial operations. An ERP system frees up the need for manual data entry and other time-consuming tasks by incorporating different systems and apps that a finance department employs into a single, unified platform, saving both money and time.
4. Interpreted Procurement and Purchasing
With precise real-time data, custom manufacturers can streamline procurement processes, eliminate lead times, and bargain better deals with suppliers.
ERP software helps automate and optimize your purchasing processes: As an ERP always manages your inventory levels in the background of anything you do, you will understand what stock you have in hand, and what order is placeable to complete a job. With an ERP, you can easily create a PO with a click- rather than manually- leading to significant savings in both money and time.
ERP facilitates custom manufacturers to develop and track purchase orders automatically, eliminating the risk of errors and delays, which can result in significant cost savings. Besides, you can easily use real-time data on demand and inventory levels and accumulate POs, to bargain on better prices with your suppliers.
5. Improved Customer Relationship Management
ERP systems deliver a unified platform for custom manufacturers to look after customer interactions, right from order processing and delivery to post-sales support.
This can indirectly enhance customer satisfaction, eliminate the risk of order errors, and boost repeat business. A better understanding of customer needs can help you identify occasions of upselling and cross-selling, thereby augmenting revenue and profitability.
Conclusion
A study from Panorama Consulting discovered that the average ROI for an ERP implementation was about 168%, followed by a payback period of nearly 3.7 years- you can double your initial investment. ERPs are fool-proof investments that will enhance your company’s business on different levels.
Leverage BizSuite from Smartinfologiks- a comprehensive business management software that assists businesses in managing work in a way that everything is organised in one place. End-to-end business intelligence solutions that effortlessly integrate with different ecosystems. Schedule an appointment today for a detailed and comprehensive discussion following the best-in-class ERP solutions.